Welcome to RennTech.org Community, Guest
There are many great features available to you once you register at RennTech.org
You are free to view posts here, but you must log in to reply to existing posts, or to start your own new topic. Like most online communities, there are costs involved to maintain a site like this - so we encourage our members to donate. All donations go to the costs operating and maintaining this site. We prefer that guests take part in our community and we offer a lot in return to those willing to join our corner of the Porsche world. This site is 99 percent member supported (less than 1 percent comes from advertising) - so please consider an annual donation to keep this site running.
Here are some of the features available - once you register at RennTech.org
- View Classified Ads
- DIY Tutorials
- Porsche TSB Listings (limited)
- VIN Decoder
- Special Offers
-
OBD II P-Codes - Paint Codes
- Registry
- Videos System
- View Reviews
- and get rid of this welcome message
It takes just a few minutes to register, and it's FREE
Contributing Members also get these additional benefits:
(you become a Contributing Member by donating money to the operation of this site)
- No ads - advertisements are removed
- Access the Contributors Only Forum
- Contributing Members Only Downloads
- Send attachments with PMs
- All image/file storage limits are substantially increased for all Contributing Members
- Option Codes Lookup
- VIN Option Lookups (limited)
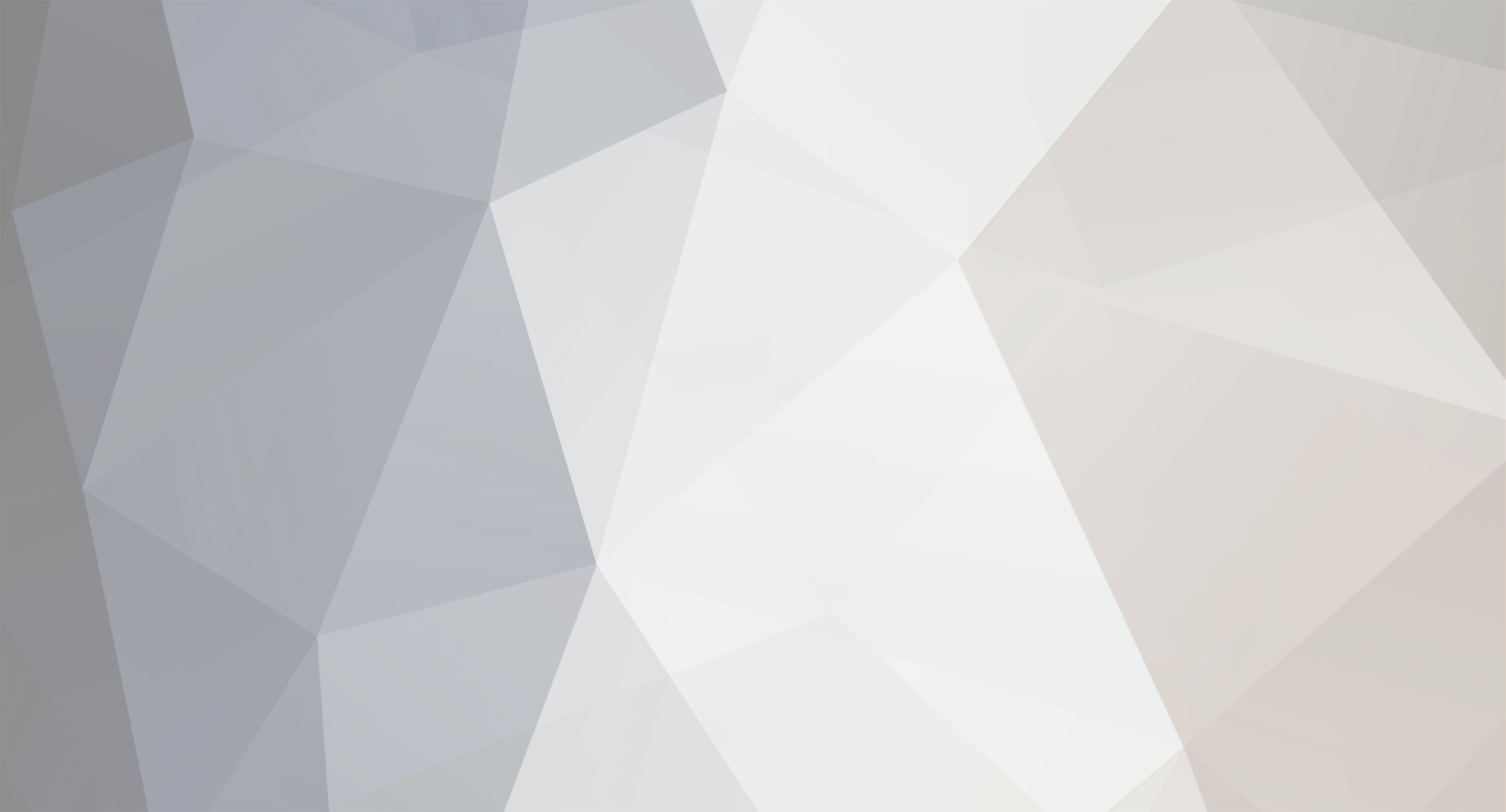
Porschelibrarian
Contributing Members-
Posts
278 -
Joined
-
Last visited
-
Days Won
2
Content Type
Profiles
Events
Forums
External Paint Colors
Downloads
Tutorials
Links Directory
Collections
Store
Everything posted by Porschelibrarian
-
PCM 2 Installation
Porschelibrarian replied to CoreyNJ's topic in DIY Articles - Carrera (996) - Accessories
But what about updating the PCM1 such as listed below from another site http://gpsunderground.com/forum/porsche/7765-porsche-pcm1-16-bit-update-2010-2011-a.html Porsche PCM1-16 bit Update 2010-2011 An update is available Opel Siemens 2010-2011 for NCDx Systems -
You can PM or email me and I can help you. You may have already noticed that Porsche made the 993 turbo manuals as a supplemental set to the 993 manuals that are on Ebay or elsewhere.
-
Porsche error codes manual
Porschelibrarian replied to ir_fuel's topic in Diagnostics, Tips and Diagnostic Tools
I presume you are looking for OBDII codes for the 997. The best thing would be to PM or email me the details and we can see what we can do. -
Need help with piwis on T30
Porschelibrarian replied to Rob001's topic in Diagnostics, Tips and Diagnostic Tools
I have always powered the KTS 520 ( and 550 ) from the car thru the USB cable, except if reprograming the alarm system as the power turns off in the car in about 30 seconds. -
Need help with piwis on T30
Porschelibrarian replied to Rob001's topic in Diagnostics, Tips and Diagnostic Tools
Are you using the standard OBDII cable? If so that is your problem as Porsche uses a different wiring scheme than all the other car makers. -
Variocam Plus
Porschelibrarian replied to tac27's topic in 996 Series (Carrera, Carrera 4, Carrera 4S, Targa)
Isn't that one of the problems that is leading to the catastrophic engine failure on the 996 engines? When the deviation doesn't match but is not enough out of range to throw a code so one keeps driving until ........... Also check if the deviation is the same at idle after reving the engine a couple of times. -
Code P0446
Porschelibrarian replied to BoxsterSenior's topic in Diagnostics, Tips and Diagnostic Tools
You need to get the full set of Porsche service manuals including the OBDII and Diagnostic manuals. You can contact me about that. As to your code see below. I copied most of the information for you and attached the pages from the DME 5.2 manual. Obviously this is only for educational purposes. P0446 95 EVAP Canister Shutoff Valve (Function) – Below Limit 20 93 P0446 95 EVAP Canister Shutoff Valve (Function) – Below Limit Function The task of the shutoff valve is to seal the purge air line to the EVAP canister during the fuel tank leak test. Diagnosis conditions – Oxygen sensing system active – No secondary air – No secondary air diagnosis – Air mass < 30 kg/h – Engine running – Vehicle speed = 0 km/h – Intake air temperature between –12 °C and 60 °C – Battery voltage > 11 V – Engine load < 2.4 ms – The vehicle must not be at an altitude of above 2448 m – Time elapsed after engine start-up > 990 sec. – No faults in: Throttle position sensor, idle air control, load sensing, misfire detection, vehicle speed, EVAP canister purge valve, idle air control valve, mass air flow sensor, voltage supply, pressure sensor, shutoff valve and engine temperature DTC No. Fault conditions Fault area P0446 Below lower limit – Purge air line blocked – Flow resistance of EVAP canister too high Note Fuel tank ventilation can be activated with the Porsche System Tester 2 in the Short test menu. On-Board Diagnostic Boxster Troubleshooting 1999 Supplement 3 P0446 - 1 System Overview 673_97 1 – EVAP canister purge valve 2 – EVAP canister 3 – Purge air 4 – Tank 5 – Pressure sensor 6 – Shutoff valve 7 – Operating purge valve 8 – To intake manifold 9 – Vacuum control valve 6 Troubleshooting Boxster On-Board Diagnostic P0446 - 2 Supplement 3 1999 Diagnosis Procedure 1 Check purge air line for blockage. OK Repair purge air line. End Replace EVAP canister. End Not OK On-Board Diagnostic Boxster Troubleshooting 1999 Supplement 3 P0446 - 3 1 Check purge air line for blockage. 1. Remove front right-hand wheel housing liner. 2. Detach purge air line (connection face up) from EVAP canister. 3. Blow through purge air line with compressed air. Troubleshooting Boxster On-Board Diagnostic P0446 986 DME 5.2 P0446.pdf -
Fault Code 1192
Porschelibrarian replied to Schmides's topic in Diagnostics, Tips and Diagnostic Tools
I have attached 2 pages from the Cayenne OBDII manuals which are included in the Cayenne service set I have. They cover the 1192 or P811 fault code you mentioned. See what your outside mechanic says. You and he will need the entire set. Obviously I am showing the pages for educational purposes only. 1192 ( P811) Cayenne Fault Code.pdf -
There is a peice from China ( where else) that claims to be able to attach to an OBDII cable and plug into the Porsche round connection. They have sent me 3 units and all 3 failed to work on a PST2 with a PIWIS and the OBDII cable. I will let you know if I find a successful cable to work a PIWIS clone on an 88 thru 95 Porsche
-
I know that the BOSCH OBDII cable is wired differently from the PORSCHE OBDII cable. Also I think there are few hardware differences inside the Porsche unit vs the Bosch unit.
-
Durametric Software.
Porschelibrarian replied to JamesD's topic in 996 Series (Carrera, Carrera 4, Carrera 4S, Targa)
Does any of the Durametric software packages reprogram the DME or alarm codes and various other on-board computer boxes, such as the airbag controls,if needed? What about programming keys? All those functions would be needed on a Cayenne, 996 or 986. -
Owners Manual. I am not aware of GT3 RS service manual - everything is in the PIWIS tester now. I looked thru the PIWIS and didn't see the RS in there. The R, RS, and RSR models are from Porsche Motorsports not Porsche of North America and have seperate workshop manuals for each year. What year GT3 RS are you looking for?
-
The 986 Workshop manuals, TSBs, wiring diagrams, OBDII manuals I have collected are updated and contain the information for all years, all models and updates thru a few months ago. Just about all the other CDs I have seen for download or on Ebay are 97 through 2000 and do not include every year wiring diagrams up till 2004 or the OBDII manuals or Diagnostic Manual as I do.
-
I thought you guys might like this. This is from Porsche on how to remove and reinstall the engine. WM 100119 Removing and installing engine Tools Designation Type Number Description Master Gear unit elevating platform Workshop equipment WE 1206 Flexible-head socket wrench, a/f 10 Special tool 9824/1 Torx Micro Bit T45 Special tool 9824/3 Spring compressor VW tool VW 552 Technical values Location Description Type Basic value Tolerance 1 Tolerance 2 Ground cable for engine to body M8 Tightening torque 10 Nm (7.5 ftlb.) Connecting nut on fuel low-pressure line Tightening torque 30 Nm (22 ftlb.) Preliminary work Preliminary work 1. Drain refrigerant from the air conditioning system. ? 870317 Draining and filling refrigerant 2. Remove cowl panel cover. ? 508719 Removing and installing cowl panel cover 3. Remove transverse control arm cover. ? 852219 Removing and installing plenum panel cover 4. Remove rear profile seal. ? 553319 Removing and installing front lid seal Removing rear profile seal 5. Drain coolant. ? 193817 Draining and filling coolant Coolant drain plug 6. Remove underbody panelling. ? 519219 Removing and installing cover for front underbody ? 519319 Removing and installing cover for centre underbody ? 519419 Removing and installing cover for rear underbody 7. Remove the cardan shaft. ? 393519 Removing and installing rear cardan shaft 8. Remove brake calliper, but do not remove the brake line. Suspend brake calliper in the wheel housing with a tie-wrap or a piece of wire. ? 473919 Removing and installing front brake calliper ? 473919 Removing and installing front brake calliper (PCCB) 9. Disconnect battery ground strap. ? 9X00IN Work instructions after disconnecting the battery 10. Remove front part of front wheel housing liner at both sides. ? 505619 Removing and installing front wheel housing liner 11. Remove front left wheel housing liner completely on vehicles with PDCC. ? 505619 Removing and installing front wheel housing liner 12. Lower the vehicle. Removing engine Removing engine Warning Caustic fluid Danger of chemical burns ? Avoid contact with caustic fluid. ? Wear personal protective gear. ? Ensure that there is good ventilation. ? If you do come into contact, wash off immediately with plenty of warm water and contact a doctor if necessary. Caution Hot components Risk of burns ? Let hot components cool down. ? Wear personal protective gear. Information These instructions describe how to remove and install the engine on vehicles with turbo engines with the maximum number of accessories and components. Some of the steps described here may not be necessary on vehicles with naturally aspirated engines or on 2WD vehicles, for example, since these vehicles do not have certain accessories and components. The slightly different illustrations between the naturally aspirated engine and the turbo engine show essentially the same tasks. 1. Remove engine wire harness in the plenum panel. 1.1. Release the relay fuse box ? Lifting up relay fuse box in the plenum panel at both sides, lift it up and disconnect the wire harness for the DME control unit in the plenum panel. Lifting up relay fuse box 1.2. Release the connector on the DME control unit -Up arrow- and disconnect it -side direction arrow- . Connector for DME control unit 1.3. Remove sealing sleeve with wire harness from the on-board panel. ? Sleeve with wire harness Sleeve with wire harness Information Before setting down removed cables, lines and components, protect the top of the engine, the intake-air distributor and the design covers from scratches using a suitable cloth. 1.4. Place engine wire harness on the engine block. Warning Highly inflammable or explosive materials Danger of fire or explosion ? Avoid contact with hot parts or sources of ignition. ? Use suction to remove ignitable vapours. ? Attach warning sign in a clearly visible position. Notice Aggressive fluids Risk of damage to components and surfaces ? Do not spill fluids. ? If a component comes into contact with the fluid, wash the component or surface with water. ? Replace components that are already damaged. 2. Disconnect fuel low-pressure line. 2.1. Release and disconnect tank ventilation and vacuum line ? Tank ventilation and vacuum line at the connection point. Tank ventilation and vacuum line 2.2. Put a cloth under the connection for the fuel low-pressure line to be disconnected in order to collect emerging fluid. 2.3. Release the fuel low-pressure line by countering with a wrench -direction arrow- and disconnect it. Counter at the centre piece and remove union nut on engine side. Fuel low-pressure line 3. Remove upper torque support. ? 103719 Removing and installing torque support 4. Disconnect plug connections for oxygen sensors at the left and right. 4.1. Release and disconnect oxygen sensor plug connection -1- ( -arrow- ) at both sides. Oxygen sensor plug connection Information Before setting down removed cables, lines and components, protect the top of the engine, the intake-air distributor and the design covers from scratches using a suitable cloth. 4.2. Place connecting cable for oxygen sensors on the engine. 5. Remove secondary-air pump. 5.1. Unscrew secondary-air pump and pull off hose. ? Removing secondary-air pump Removing secondary-air pump Information Before setting down removed cables, lines and components, protect the top of the engine, the intake-air distributor and the design covers from scratches using a suitable cloth. 5.2. Place the secondary-air pump on the engine and secure it with a tie-wrap to prevent it from falling down. 6. Pull vacuum line off the vacuum pump at the connection piece -direction arrow- . Vacuum pump hose 7. Release clip on coolant hoses at the plenum panel and remove them from the connection point at the plenum panel (cross panel). ? Removing coolant hoses Removing coolant hoses Information Before setting down removed cables, lines and components, protect the top of the engine, the intake-air distributor and the design covers from scratches using a suitable cloth. 8. Pull breather hose off the bleeder valve -direction arrow- and set it down on the engine. Breather hose 9. Remove positive cable at the jump-lead starting point. 9.1. Release flap on jump-lead starting point. ? Jump-lead starting point Jump-lead starting point Information Before setting down removed cables, lines and components, protect the top of the engine, the intake-air distributor and the design covers from scratches using a suitable cloth. 9.2. Unscrew positive cable for battery at the jump-lead starting point ? Jump-lead starting point and set it down on the engine. 10. Disconnect hose for coolant reservoir underneath the valve cover (cylinders 5 to 8) -direction arrow- . Hose for coolant reservoir 11. Drain hydraulic oil tank until empty. ? 430955 Replacing reservoir (PDCC) ? 489755 Replacing reservoir 12. Release and disconnect hose for hydraulic oil tank ? Hose for hydraulic oil tank . Hose for hydraulic oil tank 13. Remove air box on throttle valve. 13.1. Remove design cover. ? 108319 Removing and installing engine cover (design cover) 13.2. Unscrew bayonet bolt at the air box -direction arrows- . Bayonet bolt 13.3. Release and unplug connector for boost pressure sensor -position arrow- . Connector for boost pressure sensor 13.4. Release hose clamps -position arrows- on the air box at both sides. Hose clamps 13.5. Pull the air box out of the retaining clip, but leave the ventilation line (underneath the air box) for the crankcase fitted. Information Before setting down removed cables, lines and components, protect the top of the engine, the intake-air distributor and the design covers from scratches using a suitable cloth. 13.6. Set the air box down on the engine. 14. Disconnect wastegate control lines on both sides at the T-piece -direction arrow- . Wastegate control line 15. Release and disconnect the clamp on the coolant hoses on the aluminium pipes for the thermostat housing at both sides. ? Coolant hoses Coolant hoses 16. Secure coolant hoses together with the pressure hoses for the charge air cooler at the lock carrier with tie-wraps. ? Securing hoses Securing hoses 17. To relieve the control arms, fit the safety hooks -position arrow- for the upper control arm at both sides. Spring compressor VW 552 Safety hooks 18. Raise the vehicle halfway. ? 4X00IN Lifting the vehicle 19. Release and disconnect plug connection for rpm sensor at the wheel carrier on both sides -direction arrow- . Connector for rpm sensor 20. Remove chassis components. 20.1. Remove fastening nuts -1- on the upper control arms at both sides -direction arrow- . Fastening nuts on upper control arms 20.2. Remove fastening nut on connecting link at the spring strut on both sides -direction arrow- . Fastening nut on connecting link 20.3. Loosen fastening nuts -1- on the lower control arm at both sides, but do not remove the bolt yet. Fastening nuts on lower control arms 21. Left wheel housing: Remove fastening nut on power-steering pressure line holder and detach the retaining eyelet ? Fastening nut on holder . Fastening nut on holder Information Working with steel flexi-pipes Steel flexi-pipes are particularly prone to kinking and pinching. Be particularly careful with steel flexi-pipes during removal, storage and reinstallation. Mark the installation position of the pipe with a paint marker during removal. Steel flexi-pipes must never be installed twisted. 22. Left wheel housing: Disconnect steel flexi-pipes on the PDCC valve block at the front. 22.1. Mark the installation position of the steel flexi-pipes -2- on the steel flexi-pipes themselves and on the valve block using a suitable paint marker -3- . 22.2. Unscrew cap screws on steel flexi-pipes -1- . Steel flexi-pipes 23. Right wheel housing: Remove fastening screw -arrow- on the ground cable for the engine at the front right frame carrier. Ground cable 24. Raise the vehicle fully. ? 4X00IN Lifting the vehicle 25. By carefully releasing the tension lock, disconnect the pressure hose on the charge air cooler at both sides ? Pressure hose on charge air cooler and leave the hose hanging freely. Pressure hose on charge air cooler 26. Press the pressure hose aside at both sides, disconnect the hose clamp -position arrow- fitted behind it on the suction hose and pull off the hose -direction arrow- . Suction hose 27. Remove ambient air valves at both sides. Ambient air valve 27.1. Disconnect ambient air valve at the suction hose -1- on both sides. 27.2. Disconnect ambient air valve at the pressure hose -2- on both sides. 27.3. Disconnect vacuum line -3- on the ambient air valve on both sides and remove ambient air valve. Information Working with steel flexi-pipes Steel flexi-pipes are particularly prone to kinking and pinching. Be particularly careful with steel flexi-pipes during removal, storage and reinstallation. Mark the installation position of the pipe with a paint marker during removal. Steel flexi-pipes must never be installed twisted. 28. Left side: Loosen steel flexi-pipe to the expansion hose ? Steel flexi-pipe to expansion hose . 28.1. Mark the installation position of the steel flexi-pipes on the steel flexi-pipes themselves and on the valve block using a suitable paint marker. 28.2. Loosen steel flexi-pipe to the expansion hose -direction arrow- and disconnect it. Steel flexi-pipe to expansion hose 29. Left side: Remove return hose for hydraulic oil cooler. 29.1. Unscrew fastening screw -1- between the hose clamps. 29.2. Disconnect return hose -2- at the hydraulic oil cooler. Return hose for hydraulic oil cooler 30. Remove reinforcement plate -1- . Reinforcement plate 30.1. Unscrew fastening screws -2- . 30.2. Remove reinforcement plate -1- . Notice Opened refrigerant system for repairs. Moisture penetrated into the refrigerant system. Soiling of refrigerant circuit. Saturation and subsequent disintegration of dryer. If the dryer has disintegrated, the dryer, compressor and evaporator may be damaged. ? If the air humidity is too high and if the refrigerant circuit is open for some time, it will be necessary to replace the dryer. Information After disconnecting hoses, close off all openings immediately using commercially available rubber stoppers. When fitting parts, do not remove stoppers until shortly before installation. Likewise, do not remove the protective foil from the dryer until just before installation. The dryer absorbs moisture from the air and is then useless. 31. Remove air-conditioning compressor accessories. Flexible-head socket wrench, a/f 10 9824/1 Torx Micro Bit T45 9824/3 31.1. Remove intake pipe and pressure line from the air conditioning compressor. ? Air-conditioning compressor lines Air-conditioning compressor lines 31.2. Loosen fastening screw -1- on air-conditioning line holder. Air-conditioning line holder (at the front of the supporting frame) 31.3. Remove air-conditioning line holder from the guide -2- . 32. Remove PDK wiring harness. 32.1. Remove fastening screws -position arrows- on heat protection panel for PDK wiring harness on the transmission. Heat protection panel for PDK wiring harness 32.1.1. Remove heat protection panel for PDK wiring harness. 32.2. Release and unplug the connectors on the end of the PDK wiring harness at the transmission -1- ( -2- ) and loosen the retaining clip -3- . Connectors on PDK wiring harness 32.3. Loosen the retaining clips on the PDK wiring harness and remove the PDK wiring harness from the clips -position arrows- . Retaining clips on PDK wiring harness 33. Remove parking lock cable. ? 371319 Removing and installing locking cable 33.1. Disconnect the parking lock cable from the ball joint on the transmission. 33.2. Lift the parking lock cable out of the support and secure it towards the top. 34. Remove heat protection panel -1- between the universal joint for the steering gear and the primary catalytic converter. Heat protection panel 34.1. Remove fastening screws -2- . 34.2. Remove heat protection panel -1- . Information Fix steering wheel with wheels in straight-ahead position (engage steering column lock or clamp steering wheel in centre position with steering wheel holder). If this is not done, the airbag contact unit will have to be put in the centre position after installation of the steering gear ? 945019 Removing and installing steering column switch 35. Remove universal joint -1- . Removing universal joint 35.1. On vehicles with Servotronic: Pull off connector -3- . 35.2. Loosen holder on Servotronic connector cable and set the cable aside. 35.3. Loosen clamping screw -2- . 35.4. Slide universal joint -1- and lower part of steering column upwards. Warning ATF! Possible danger of injury or damage (swollen hoses, skin irritation, danger of slipping, etc.) ? Before lines are opened, place a cloth underneath them! ? Components that come into contact with ATF must be cleaned IMMEDIATELY with water! ? Take suitable protective measures (e.g. gloves, safety goggles, oil binding material) ? Collect emerging ATF! 36. Loosen supply and return hose for the ATF transmission fluid cooler -direction arrows- and drain the fluid. Supply and return hose for transmission fluid cooler Information Before moving the lifting platform, mark the position of the wheels on the workshop floor with a piece of chalk. This makes it easier to position the platform again for re-installation. 37. Place elevating platform Master Gear unit elevating platform WE 1206 under the vehicle and move all assembly drivers -A, B, C, D, E, F- to the same height at the correct position. Overview of assembly drivers For specific tightening torques and further details on positioning, see the operating instructions provided with the assembly fixture: Assembly fixture for Porsche Panamera Master Gear 1.0 elevating platform Legend for assembly drivers and supports Position Designation Explanation A Transmission bracket For mounting on the transmission mount. B Assembly driver on cross panel For mounting on the cross panel. C Wheel hub holder Secures the axles and prevents them from falling out. D Steering knuckle bracket In conjunction with the wheel hub holder C, this protects the axles and spring struts from damage. E Assembly driver on front-axle carrier For mounting on the rear of the front-axle carrier. F Front-axle carrier support For mounting on the front of the front-axle carrier. 38. Get the elevating platform ready and move it to the jacking points on the front axle (supporting frame and even transmission mount). Set the heights of the drivers and supports and ensure solid contact. 39. Remove bolts on lower control arms. 39.1. Raise the elevating platform slightly in order to relieve the pressure on the bolts on the lower control arms. 39.2. Pull out bolt on the lower control arm on both sides -direction arrow- . Bolts on lower control arms 40. Remove the safety hooks -position arrow- for the upper control arm on both sides. Safety hooks 41. Detach front-axle carrier. Marking and fastening screws on front-axle carrier 41.1. Mark the position of the contact points of the front-axle carrier on the longitudinal members -position arrow- on both sides. 41.2. Remove fastening screws securing front-axle carrier to the longitudinal member on both sides. 42. Remove fastening screws -position arrows- securing the anti-roll bar mount to the supporting plate on both sides. Fastening screws on supporting plate 43. Remove transverse struts. Removing struts (right side shown here) 43.1. Right side: Press rear wheel housing cover -1- down -direction arrow- and remove the transverse strut -2- between the supporting plate and door sill. 43.2. Left side: Remove transverse strut between the supporting plate and door sill. 44. Fit wheel hub holder -1- at both sides using assembly pins -2- on the wheel hub. Wheel hub holder (shown here on steel brake disc) 45. Remove the fastening screws -position arrows- on the rear transmission mount. Fastening screws on transmission mount Information When lowering the engine, make sure that cables or lines do not get mounted accidentally between engine and body. Thus a second person should make sure that the cables and lines do not get caught. Information Before moving the lifting platform, mark the position of the wheels on the workshop floor with a piece of chalk. This makes it easier to position the platform again for re-installation. 46. Remove the engine. 46.1. Gradually lower the elevating platform Master Gear unit elevating platform WE 1206 and engine/transmission unit. 46.2. Gradually guide the air-conditioning lines ? Air-conditioning line along with your hand. Air-conditioning line 46.3. Move engine out from under the vehicle using the elevating platform. Installing engine Installing engine Warning ATF! Possible danger of injury or damage (swollen hoses, skin irritation, danger of slipping, etc.) ? Before lines are opened, place a cloth underneath them! ? Components that come into contact with ATF must be cleaned IMMEDIATELY with water! ? Take suitable protective measures (e.g. gloves, safety goggles, oil binding material) ? Collect emerging ATF! Notice Opened refrigerant system for repairs. Moisture penetrated into the refrigerant system. Soiling of refrigerant circuit. Saturation and subsequent disintegration of dryer. If the dryer has disintegrated, the dryer, compressor and evaporator may be damaged. ? If the air humidity is too high and if the refrigerant circuit is open for some time, it will be necessary to replace the dryer. Information Fix steering wheel with wheels in straight-ahead position (engage steering column lock or clamp steering wheel in centre position with steering wheel holder). If this is not done, the airbag contact unit will have to be put in the centre position after installation of the steering gear ? 945019 Removing and installing steering column switch Information The tightening specifications for the basic engine are stored centrally. ? 1001IN Tightening torques, tightening sequences, assembly overviews. Tightening torques and assembly instructions for other affected assemblies (e.g. chassis, electrics, transmission or body) or for peripheral engine equipment can be found in the corresponding documents. Information Due to currently correct tightening specifications, the screw specifications can be found in the corresponding repair descriptions for the assemblies chassis, transmission, electrics, etc. 1. Guide the engine in under the vehicle. Information Check the position of all lines, hoses and cables again during and following installation. Make sure that: The lines, hoses and cables are not installed twisted (markings on steel flexi-pipes!) The lines, hoses and cables are not exposed to any mechanical strain from the outside while driving, i.e. they must not be over-strained or deformed. The lines, hoses and cables are not rubbing against other moving components. The lines, hoses and cables cannot become clamped. 1.1. Move engine under the vehicle using the elevating platform. 1.2. Position the wheels of the elevating platform at the position marked during removal. 1.3. Guide the engine up into the engine compartment using the lifting equipment. 1.4. Gradually guide the air-conditioning lines ? Air-conditioning line along with your hand. Air-conditioning line 1.5. Fit the parking lock cable at half height (easier to access). ? 371319 Removing and installing locking cable 1.5.1. Pull the parking lock cable down and engage it in the support. 1.5.2. Fit the parking lock cable at the ball joint on the transmission. 2. Fit the front-axle carrier. For tightening torques and other details, see: ? 400619 Removing and installing front-axle carrier Marking and fastening screws on front-axle carrier 2.1. By adjusting the position of the elevating platform slightly, move to the marking -position arrow- for the contact points for the front-axle carrier on the longitudinal members. 2.2. Fit the fastening screws securing front-axle carrier to the longitudinal member on both sides. 3. Fit the fastening screws -position arrows- on the rear transmission mount. For tightening torques and other details, see: ? 343519 Removing and installing transmission Fastening screws on transmission mount 4. Fit fastening screws -position arrows- securing the anti-roll bar mount to the supporting plate on both sides. For tightening torques and other details, see Chassis Fastening screws on supporting plate 5. Fit transverse struts -2- . For tightening torques and other details, see Chassis. Removing struts (right side shown here) 5.1. Right side: Press rear wheel housing cover -1- down -direction arrow- and fit the transverse strut -2- between the supporting plate and door sill. 5.2. Left side: Fit transverse strut between the supporting plate and door sill. 6. Guide in and fit bolt on the lower control arm -direction arrow- . For tightening torques and other details, see: ? 4X00IN00 Tightening torques for front axle Bolts on lower control arms 7. Remove wheel hub holder -1- on the elevating platform and remove assembly pins -2- on the wheel hub. Wheel hub holder (shown here on steel brake disc) 8. Lower the elevating platform and push it away. Warning ATF! Possible danger of injury or damage (swollen hoses, skin irritation, danger of slipping, etc.) ? Before lines are opened, place a cloth underneath them! ? Components that come into contact with ATF must be cleaned IMMEDIATELY with water! ? Take suitable protective measures (e.g. gloves, safety goggles, oil binding material) ? Collect emerging ATF! 9. Fit supply and return hose for the ATF transmission fluid cooler -direction arrow- . For tightening torques and other details, see: ? 386019 Removing and installing ATF cooler Supply and return hose for transmission fluid cooler Information Fix steering wheel with wheels in straight-ahead position (engage steering column lock or clamp steering wheel in centre position with steering wheel holder). If this is not done, the airbag contact unit will have to be put in the centre position after installation of the steering gear ? 945019 Removing and installing steering column switch 10. Fit universal joint -1- . For tightening torques and other details, see: ? 481519 Removing and installing steering column Fitting universal joint 10.1. Pull universal joint -1- and lower part of steering column downwards -direction arrow- . 10.2. Fit clamping screw -2- . 10.3. On vehicles with Servotronic: Plug in connector -3- . 10.4. Fit holder on cable for Servotronic connector. 11. Fit heat protection panel -1- between the universal joint for the steering gear and the primary catalytic converter. Heat protection panel 11.1. Guide in heat protection panel -1- . 11.2. Fit the fastening screws -2- . 12. Fit PDK wiring harness. 12.1. Plug in the connectors on the end of the PDK wiring harness at the transmission -2- ( -1- ) and fit the retaining clip -3- . Connectors on PDK wiring harness 12.2. Fit retaining clips -position arrows- for the PDK wiring harness. Retaining clips on PDK wiring harness 12.3. Guide in heat protection panel for PDK wiring harness and fit fastening screws -position arrows- on the transmission. Heat protection panel for PDK wiring harness Notice Opened refrigerant system for repairs. Moisture penetrated into the refrigerant system. Soiling of refrigerant circuit. Saturation and subsequent disintegration of dryer. If the dryer has disintegrated, the dryer, compressor and evaporator may be damaged. ? If the air humidity is too high and if the refrigerant circuit is open for some time, it will be necessary to replace the dryer. 13. Fit air-conditioning compressor accessories. Flexible-head socket wrench, a/f 10 9824/1 Torx Micro Bit T45 9824/3 For tightening torques and other details, see: ? 873419 Removing and installing air-conditioning compressor 13.1. Fit intake pipe and pressure line -1 and 2- on the air conditioning compressor. Air-conditioning compressor lines 13.2. Guide air-conditioning line holder into the guide -2- . Air-conditioning line holder 13.3. Fit fastening screw -1- on air-conditioning line holder. 14. Fit reinforcement plate -1- . For tightening torques and other details, see: ? 400619 Removing and installing front-axle carrier Reinforcement plate 14.1. Position reinforcement plate -1- . 14.2. Screw in fastening screws -2- . 15. Left side: Fit return hose for hydraulic oil cooler. 15.1. Fit return hose -2- at the hydraulic oil cooler. Return hose for hydraulic oil cooler 15.2. Screw in fastening screw -1- between the hose clamps. Information Working with steel flexi-pipes Steel flexi-pipes are particularly prone to kinking and pinching. Be particularly careful with steel flexi-pipes during removal, storage and reinstallation. Mark the installation position of the pipe with a paint marker during removal. Steel flexi-pipes must never be installed twisted. 16. Left side: Fit steel flexi-pipe to the expansion hose. ? Steel flexi-pipe to expansion hose 16.1. Fit steel flexi-pipe to the expansion hose in line with the marking applied during removal. Steel flexi-pipe to expansion hose 17. Fit ambient air valves. Ambient air valve 17.1. Fit ambient air valve at the suction hose -1- on both sides. 17.2. Fit ambient air valve at the pressure hose -2- on both sides. 17.3. Fit vacuum line -3- for the charge air cooler at both sides. 18. Fit suction hose -direction arrow- by tightening the hose clamps -position arrow- . Suction hose 19. Fit pressure hose on the charge air cooler at both sides. ? Pressure hose on charge air cooler Pressure hose on charge air cooler 20. Lower the vehicle halfway. 21. Right wheel housing: Fit fastening nut -position arrow- on the ground cable for the engine at the front right frame carrier. ? Tightening torque: 10 Nm (7.5 ftlb.) Ground cable Information Working with steel flexi-pipes Steel flexi-pipes are particularly prone to kinking and pinching. Be particularly careful with steel flexi-pipes during removal, storage and reinstallation. Mark the installation position of the pipe with a paint marker during removal. Steel flexi-pipes must never be installed twisted. 22. Fit steel flexi-pipes on the PDCC valve block at the front. 22.1. The installation position of the steel flexi-pipes -2- was marked on the steel flexi-pipes themselves and on the valve block during removal using a paint marker -3- . 22.2. Fit cap screws on steel flexi-pipes -1- and screw them in until the markings are aligned. Steel flexi-pipes 23. Left wheel housing: Fit fastening nut on holder for power-steering pressure line. ? Fastening nut on holder Fastening nut on holder 24. Fit chassis components. 24.1. Fit fastening nuts -1- on the upper control arms at both sides. Fastening nuts on upper control arms 24.2. Fit fastening nut on connecting link at the spring strut on both sides -direction arrow- . Fastening nut on connecting link 24.3. Fit fastening nut -1- on the lower control arm at both sides. Fastening nuts on lower control arms 25. Connect plug connection for rpm sensor on both sides. ? Connector for rpm sensor Connector for rpm sensor 26. Disconnect the secured coolant hoses and pressure hoses on the charge air cooler from the lock carrier. ? Hoses secured to the lock carrier Hoses secured to the lock carrier 26.1. Fit the coolant hoses on the engine block at both sides. ? Coolant hoses Coolant hoses 27. Connect wastegate control lines on both sides at the T-piece -direction arrow- . Wastegate control line 28. Fit air box on throttle valve. 28.1. Fit hose clamps -position arrows- on the air box at both sides. Hose clamps 28.2. Fit bayonet bolt at the air box -direction arrows- . Bayonet bolt 28.3. Plug in connector for boost-pressure sensor -position arrow- . Connector for boost pressure sensor 28.4. Install design cover. ? 108319 Removing and installing engine cover (design cover) 29. Fit hose for hydraulic oil tank. ? Hose for hydraulic oil tank Hose for hydraulic oil tank 30. Fit hose for coolant reservoir -direction arrow- . Hose for coolant reservoir 31. Fit positive cable at the jump-lead starting point. 31.1. Release flap on jump-lead starting point. ? Jump-lead starting point Jump-lead starting point 31.2. Fit positive cable for the battery at the jump-lead starting point. 31.3. Lock the flap for the jump-lead starting point. 32. Fit breather hose on the bleeder valve ? Breather hose . Breather hose 33. Guide coolant hoses into the connection point and lock with the clip. ? Fitting coolant hoses Fitting coolant hoses 34. Fit secondary-air pump and hose. ? Fitting secondary air pump ? 266519 Removing and installing secondary-air pump with bracket Fitting secondary air pump 35. Connect plug connections for oxygen sensors -1- at both sides. Oxygen sensor plug connection 36. Install upper torque support. ? 103719 Removing and installing torque support Notice Aggressive fluids Risk of damage to components and surfaces ? Do not spill fluids. ? If a component comes into contact with the fluid, wash the component or surface with water. ? Replace components that are already damaged. Warning Highly inflammable or explosive materials Danger of fire or explosion ? Avoid contact with hot parts or sources of ignition. ? Use suction to remove ignitable vapours. ? Attach warning sign in a clearly visible position. 37. Fit fuel low-pressure line. 37.1. Fit tank ventilation and vacuum line ? Tank ventilation and vacuum line . Tank ventilation and vacuum line 37.2. Fit the fuel low-pressure line by countering with a wrench. Counter at the centre piece and fit union nut on engine side. ? Tightening torque: 30 Nm (22 ftlb.) ? Fuel low-pressure line Fuel low-pressure line 38. Install wiring harness in the plenum panel. 38.1. Fit sleeve with wire harness into the on-board panel. ? Sleeve with wire harness Sleeve with wire harness 38.2. Release the relay fuse box in the plenum panel at both sides, lift it up ? Lifting up relay fuse box and route wire harness for the DME control unit underneath in the plenum panel. Lifting up relay fuse box 38.3. Engage the locking lugs for the relay fuse box in the plenum panel. 38.4. Plug in connectors on the DME control unit. Subsequent work Subsequent work Information Following replacement of the high-pressure pump and engine, the values for the high-pressure adaptation must be reset using the PIWIS Tester. Then carry out a test and adaptation drive. Read the information in the section ? 24701900 Removing and installing DME (DFI) control unit. The current software must be installed on the control unit if necessary. Following conversion to a new engine, it is possible that an old software version may still be installed on the control unit. 1. Install front left wheel housing liner completely on vehicles with PDCC. ? 505619 Removing and installing front wheel housing liner 2. Install front part of front wheel housing liner at both sides. ? 505619 Removing and installing front wheel housing liner 3. Install brake calliper on both sides. ? 473919 Removing and installing front brake calliper ? 473919 Removing and installing front brake calliper (PCCB) 4. Install cardan shaft. ? 393519 Removing and installing rear cardan shaft 5. Install underbody panelling. ? 519219 Removing and installing cover for front underbody ? 519319 Removing and installing cover for centre underbody ? 519419 Removing and installing cover for rear underbody 6. Install rear profile seal. ? 553319 Removing and installing front lid seal 7. Install transverse control arm cover. ? 852219 Removing and installing plenum panel cover 8. Install cowl panel cover. ? 508719 Removing and installing cowl panel cover 9. Connect battery ground strap. ? 9X00IN Work instructions after disconnecting the battery 10. Fill in coolant. ? 193817 Draining and filling coolant 11. Fill in refrigerant for the air conditioning system. ? 870317 Draining and filling refrigerant 12. Fill the hydraulic oil tank. ? 430955 Replacing reservoir (PDCC) ? 489755 Replacing reservoir 13. Bleed power steering. ? 480201 Checking hydraulic fluid (fluid level) 14. Check ATF level. ? 370235 Checking and topping up ATF 15. Check engine-oil level. ? 170101 Checking engine-oil level 16. Perform suspension alignment. ? 449503 Suspension alignment, complete 17. Adjust the locking cable. ? 370015 Adjusting locking cable 18. Test drive the vehicle. Check the fluid level in the reservoir after the coolant circuit has cooled again and fill up to the max marking with coolant if necessary. ------------------------------------------------------
-
Removing and Installing engine I thought you guys might like this. This is from Porsche on how to remove and reinstall the engine. WM 100119 Removing and installing engine Tools Designation Type Number Description Master Gear unit elevating platform Workshop equipment WE 1206 Flexible-head socket wrench, a/f 10 Special tool 9824/1 Torx Micro Bit T45 Special tool 9824/3 Spring compressor VW tool VW 552 Technical values Location Description Type Basic value Tolerance 1 Tolerance 2 Ground cable Author Porschelibrarian Category Panamera (970) - Maintenance Submitted 01/08/2010 11:27 AM
-
Does the Bentley manual have 70 pages for the wiring diagrams? How about the OBDII codes, computer module locations in the Cayenne or the Touareg? Does it cover any body work? Transmissions? Chassis? Electronics? I know from other Bentley manuals and the VW Workshop manuals contained in Elsawin ( the VW Audi edition similar to POSES) that they are not anywhere as comprehensive as the Porsche WSM. The Workshop manual for the Cayenne is over 10,000 pages. How many pages arecontained in the Bentley manual? In addition to the WSM I have collected the Cayenne OBDII manual, Diagnostic manual, 4 years of wiring diagrams, plus complete parts information for each year and more.
-
Why would you want 3rd party abbreviated stuff when you can get the actual Porsche factory workshop manuals, or OBDII manuals plus Technical Service Bulletins and more. The Porsche factory workshop manuals are usually 10 to 15 times larger and extremely more comprehensive. If you want the most complete service information on the 996 PM or email me. I have attached a few pages. The workshop manual alone has about 4,000 more pages plus the wiring diagrams plus the .. well I am sure you get the idea. 996oilchange.pdf
-
There are no "aftermarket" repair/service manuals. There are the Porsche factory workshop manuals, OBDII manuals but Porsche has not printed them in about 5 years. If you want service manuals, part information and more send me an email or PM and can help you. I have attached a small sample for you to check out. 9PA_GROUP_0_GENERAL.pdf